Entwicklungsumgebung für Zahnradpumpen
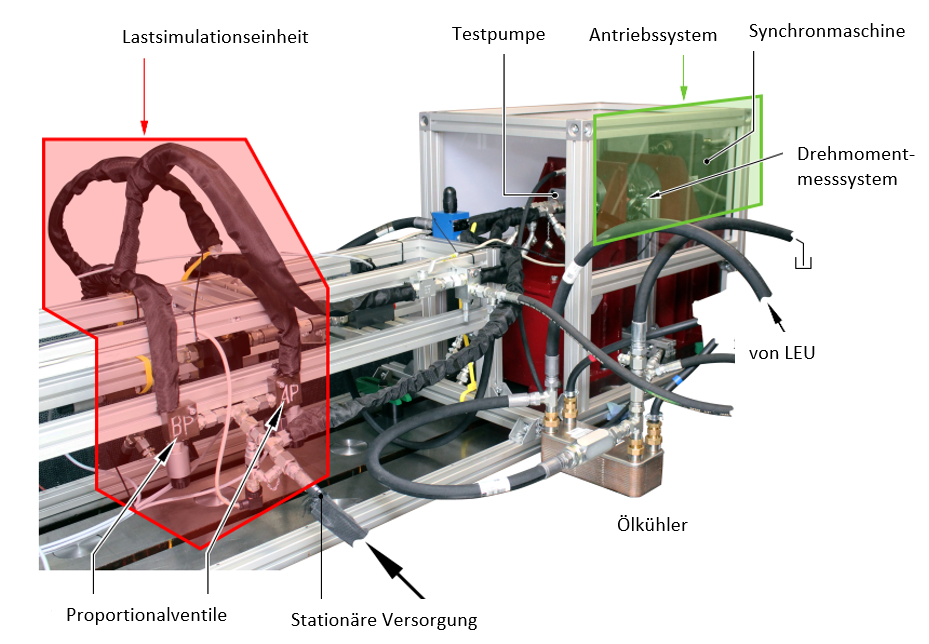
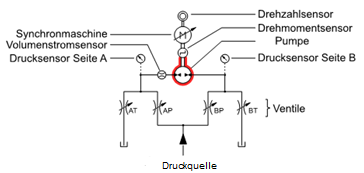
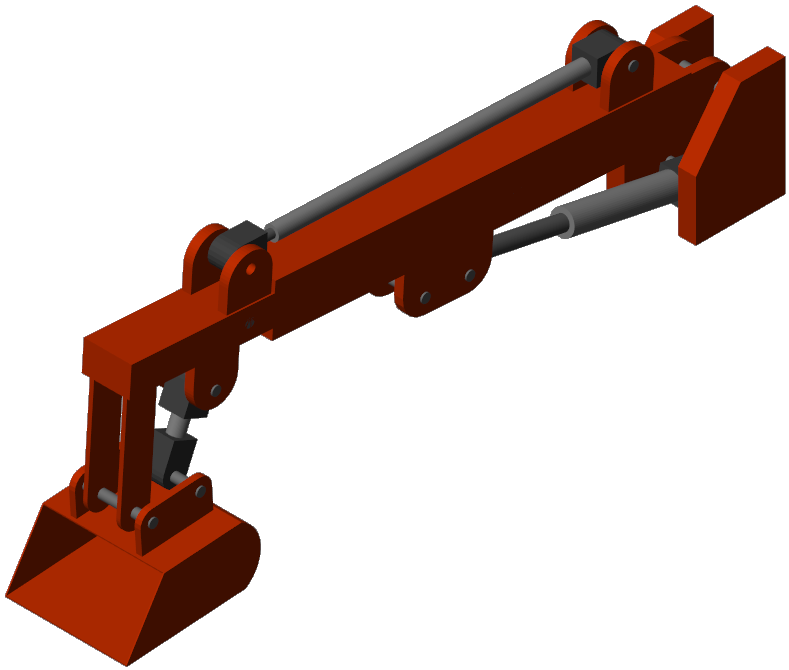
Im Rahmen des Verbundprojektes „Next Generation Innenzahnradpumpe (NeGInza)“ wurde ein Hardware-in-the-Loop-Prüfstand (HiL-Prüfstand) entworfen und umgesetzt, der als Entwicklungsumgebung für Zahnradpumpen dient. Der Fokus liegt dabei auf Untersuchungen mit einer hohen Druck-/Drehzahldynamik sowie schnellen Wechseln zwischen den Quadranten und Betriebsmodi der zu testenden Pumpe. Der Prüfstand umfasst einen Pumpenantrieb und eine Lastsimulationseinheit (LEU), welche die Drücke an beiden Pumpenanschlüssen unabhängig voneinander und mit hoher Dynamik einstellt.
Ziel ist eine realitätsnahe und anwendungsspezifische Nachbildung von Testzyklen sowie Anwendungsfällen für die Pumpe. Es ist möglich, die Zahnradpumpen unter realistischen Bedingungen zu testen und beispielsweise die Haltbarkeit bei dynamischen Lastwechseln zu optimieren. Die Druck- und Drehzahlverläufe können über der Zeit vorgegeben oder in Echtzeit anhand des Hardware-in-the-Loop-Modells (HiL-Modells) einer Anwendung ermittelt werden.
HiL-Prüfstand für Zahnradpumpen
Der Antrieb der zu prüfenden Pumpe erfolgt über eine Synchronmaschine (Servomotor), die von einem Frequenzumrichter versorgt wird Es sind sowohl ein Motor- als auch ein Generatorbetrieb möglich. Zusätzlich ist ein Drehmomentmesssystem zwischen Motor und Pumpe angebracht. Die Lastsimulationseinheit stellt eine hydraulische Brückenschaltung dar, bestehend aus vier identischen Proportionalventilen und einem Hydraulikaggregat als Konstantdruckquelle.
Die Druckregelung bzw. Ansteuerung der Proportionalventile, die Kommunikation mit dem Frequenzumrichter sowie das Erfassen von Messdaten erfolgt über eine eigenentwickelte Prüfstandssteuerung auf Basis des Echtzeitsteuerungssystems TwinCAT® der Beckhoff Automation GmbH & Co. KG. Die standardmäßige Abtastrate beträgt 4 kHz, Messgrößen lassen sich mit bis zu 50 kHz aufnehmen.
HiL-Modell
Verschiedenste Anwendungsfälle bzw. Maschinen lassen sich mittels HiL-Modell nachbilden und in Echtzeit in der Prüfstandssteuerung simulieren. Rückwirkungen der virtuellen Maschine sowie deren Hydraulikkreis werden dann von der Lastsimulationseinheit (LEU) nachgebildet und der Pumpe eingeprägt. Die Pumpe kann somit im Verbund mit der virtuellen Maschine getestet werden, was realitätsnahe Untersuchungen ermöglicht.
Beispielhaft wurde das HiL-Modell für einen Auslegerarm eines Teleskopladers erstellt. Das Modell enthält den anwendungsspezifischen Hydraulikkreislauf sowie die Aktuatoren (im Beispiel die Hydraulikzylinder des Arms). Somit lassen sich aus den Arbeits- und Aktuatorzyklen die Pumpenarbeitszyklen realitätsnah und reproduzierbar darstellen und am Prüfstand der zu testenden Pumpe einprägen.